Spot repair in ATEX-zones
Carrying out spot repairs in ATEX zones comes with strict safety regulations and operational challenges. Whether addressing corrosion, coating damage, or minor structural repairs, using conventional tools can create ignition risks, requiring hot work permits and extended downtime. With non-sparking tools, you can safely perform spot repairs without disrupting production or compromising safety.
Minimize risk, maximize efficiency
Did you know that even minor surface damage in ATEX zones can lead to long-term corrosion and expensive repairs? Spot repair is a crucial maintenance practice that prevents small issues from escalating into major structural failures. However, working in ATEX environments requires precision and strict adherence to safety guidelines.
Ensure compliance and efficiency in ATEX zones! Request a free consultation today.
The challenge: performing spot repairs in explosive environments
Performing spot repairs in ATEX zones requires a balance between safety, efficiency, and compliance. Traditional grinding, cutting, and coating removal methods generate sparks, increasing the risk of ignition. Additionally, obtaining hot work permits leads to significant downtime, delaying maintenance schedules.
Common challenges:
- Risk of explosions due to sparks from conventional tools.
- Lengthy downtime while waiting for hot work permits.
- Inefficient surface preparation affecting coating adhesion.
- Restricted access to confined spaces and high-risk areas.
The solution? Non sparking tools for spot repairs
Allmet Safety Tools offers a range of ATEX-certified, non-sparking tools designed specifically for spot repair tasks. These tools allow maintenance teams to perform efficient, high-quality repairs without ignition risks or unnecessary downtime.
Want to reduce downtime and perform safer repairs? Contact us for a product demo!
Why choose non-sparking tools for spot repair?
- No sparks, no risk – Crafted from beryllium-copper and aluminum-bronze alloys to prevent ignition hazards.
- No need for hot work permits – Complete repairs faster without waiting for approval.
- Optimized for surface preparation – Ensure strong adhesion for coatings and corrosion protection.
- Safe for confined spaces – Work safely in fuel tanks, pipelines, and restricted areas.
- Cost-effective and durable – Minimize maintenance costs with long-lasting tools.
Essential tools for spot repair in ATEX Zones
Allmet Safety Tools provides non-sparking solutions tailored for spot repair applications:
- A-0300 Combined Cutting and Weld Removal Solution – Ideal for removing corroded or damaged sections safely.
- A-0044 Spark-Free Grinding Kit – Perfect for smoothing surfaces and preparing for coatings.
- A-0057 All-Around Burr Set – Designed for precise material removal in detailed repair work.
- A-0108 ATEX Pneumatic Angle Grinder – A powerful, non-sparking solution for efficient grinding and polishing.
- A-0500 Spark-Free Paint and Coating Removal Disc – The safest way to strip coatings without ignition risks.
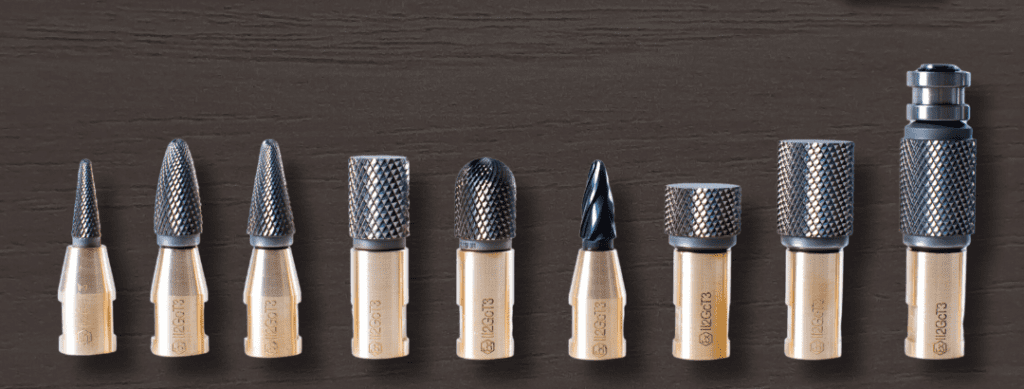
Did you know?
- Surface preparation accounts for up to 80% of coating failures, making proper spot repair critical.
- Using the right tools can reduce maintenance costs by 30%, avoiding premature replacements.
- A single spark in an ATEX zone can cause a chain reaction, emphasizing the need for non-sparking solutions.
Take the next step toward safer and more efficient spot repairs
Spot repairs are essential for extending equipment lifespan and maintaining operational integrity in ATEX zones. With Allmet Safety Tools, you can perform maintenance work safely, efficiently, and without unnecessary downtime.
Let’s optimize your spot repair process! Contact us today for expert advice or schedule a free demo to see our tools in action.
Stay safe. Stay efficient. Choose Allmet Safety Tools!