Ship maintenance and tank facilities
Maintaining ships and tank facilities in ATEX zones is no easy task. The presence of flammable gases, vapors, and combustible materials makes traditional maintenance methods risky, time-consuming, and expensive. Safety regulations require strict compliance, and the need for hot work permits often results in costly downtime. However, with the right non-sparking tools, ship and tank maintenance can be carried out safely, efficiently, and without unnecessary interruptions.
Minimizing risks in ship and tank maintenance
Did you know that over 90% of global trade relies on maritime transport? With thousands of ships and tank facilities operating daily, maintaining these assets in explosive environments presents a serious challenge. From corrosion removal to surface preparation and welding repairs, every task requires strict safety compliance to prevent ignition risks.
Ensure compliance and efficiency in ATEX zones! Request a free consultation today.
The Challenge: maintenance in high-risk ATEX environments
Ship maintenance and tank facilities operate in highly sensitive environments where fuel vapors, gases, and chemicals increase the risk of explosions. Traditional maintenance tools generate sparks, heat, and friction, requiring time-consuming hot work permits and strict monitoring. These factors lead to costly downtime and operational inefficiencies.
Common challenges:
- Risk of ignition due to sparks from grinding, cutting, or welding.
- Downtime caused by hot work permit requirements and safety procedures.
- Corrosion affecting tanks, hulls, pipelines, and key infrastructure.
- Difficulty in accessing confined spaces where ventilation is limited.
The solution: non-sparking tools for ship en tank maintenance
Allmet Safety Tools provides ATEX-certified, non-sparking solutions designed to eliminate explosion hazards and maximize efficiency. Our tools enable safe maintenance in fuel tanks, cargo holds, ballast tanks, and confined spaces without the need for hot work permits.
Want to eliminate downtime and improve safety? Contact us for a product demo!
Why clients choose our non-sparking tools:
- No sparks, no risk – Designed from beryllium-copper and aluminum-bronze alloys to eliminate ignition sources.
- No need for hot work permits – Perform essential maintenance without shutting down operations.
- Compliant with ATEX regulations – Ensure safety while meeting strict industry standards.
- Reduce downtime and maintenance costs – Complete work faster and minimize lost productivity.
- Ideal for confined spaces – Safe for enclosed areas with limited ventilation.
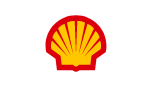
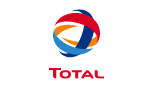
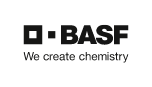
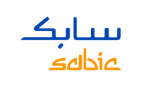
Essential tools for ship & tank maintenance
Allmet Safety Tools offers specialized non-sparking solutions for shipyards, tank farms, and offshore facilities:
- A-0300 Combined Cutting and Weld Removal Solution – For removing old welds and metal structures safely.
- A-0044 Spark-Free Grinding Kit – Ideal for surface preparation, coating removal, and corrosion treatment.
- A-0057 All-Around Burr Set – Designed for fine material removal in precision repairs.
- A-0108 ATEX Pneumatic Angle Grinder – A powerful yet safe tool for grinding in ATEX environments.
- A-0500 Spark-Free Paint and Coating Removal Disc – The perfect solution for stripping paint and coatings without sparks.
Did you know?
- A single spark can ignite fuel vapors in confined ship compartments, leading to catastrophic explosions.
- Tank facilities are among the most regulated environments due to the high risk of chemical exposure and fire hazards.
- Corrosion costs the maritime industry billions annually, making preventive maintenance crucial to operational efficiency.
Take the next step towards safer and more efficient maintenance
Managing maintenance in ATEX zones doesn’t have to mean endless delays and skyrocketing costs. With the right tools, you can take control of your operations, minimize risks, and keep your vessels and facilities running smoothly. Our non-sparking solutions provide the reliability, compliance, and efficiency you need to operate safely in hazardous environments.